In the world of pharmaceutical and medical device manufacturing, CQV (Commissioning, Qualification, and Validation) is the gateway to producing safe, compliant, and high-quality products. But as critical as CQV is, it comes with hurdles that can make even the most seasoned professionals hesitate. Managing documentation, aligning teams, and handling the never-ending compliance updates—sound familiar? We understand the challenges you face, and in this blog, we’ll dive into the top 10 obstacles in CQV and actionable strategies to overcome them.
Let’s walk through these challenges together, and by the end, you’ll have a roadmap to simplify and streamline your validation process.
1. Managing Documentation in CQV
Documentation is the backbone of CQV. Every stage, from commissioning, qualification to validating a process, requires precise documentation to ensure compliance and traceability. The challenge? It’s easy to feel buried under endless pages of documentation.
Solution: Implement digital tools for real-time updates, document version control, and easy retrieval. Standardize templates for commonly used documents, so no one is starting from scratch. Digital documentation solutions make it possible to automate compliance checks, saving you time and reducing human error.
2. Resource Allocation
Resource management is often a balancing act. Many CQV projects stall due to insufficient personnel or an overburdened team. Without the right resources, even the best project plans can fall apart.
Solution: Start with a resource assessment—identify your team’s strengths and assign roles based on expertise. Consider cross-training team members to make resource allocation more flexible. Project management tools can also help streamline communication and task assignment, keeping projects on track.
3. Risk Management
Every validation project carries risks. From equipment failures to unforeseen delays, risk management helps identify and address potential problems before they escalate. But many teams overlook it, which can lead to costly setbacks.
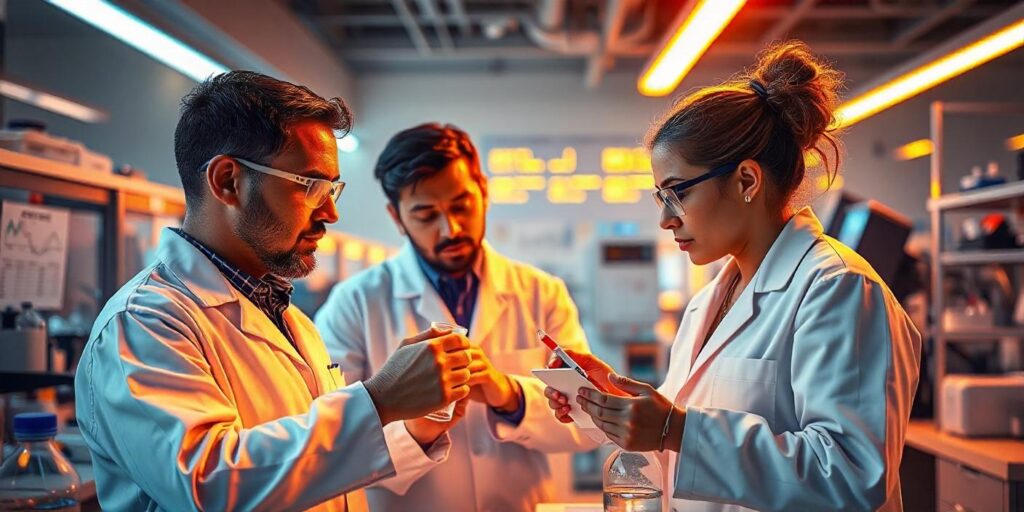
Solution: For example, in a project, a team might use Failure Modes and Effects Analysis (FMEA) to identify potential points of failure in the installation of a new system. By analyzing each stage—from installation to initial testing—they could identify a high risk of delays due to potential supply chain disruptions. With this insight, the team could then arrange alternative suppliers in advance and build in extra lead time for equipment delivery. This proactive approach helps prevent project bottlenecks, reduces downtime risk, and ensures that necessary resources are ready, minimizing the chance of costly setbacks.
4. Overcome Equipment and System Qualification Hurdles
Equipment and system qualifications are complex processes requiring detailed testing and validation. Whether it’s new machinery or software, qualifications can create bottlenecks.
Solution: Start with thorough Installation Qualification (IQ), Operational Qualification (OQ), and Performance Qualification (PQ) testing. Enlist specialists who understand your equipment, and leverage vendor documentation when available. This focused approach saves time and ensures compliance with regulatory standards.
5. Data Integrity Challenges in CQV
Data integrity is crucial in CQV. Any error in data entry or management can lead to compliance issues and product quality risks. Ensuring data accuracy across multiple systems and departments can be daunting.
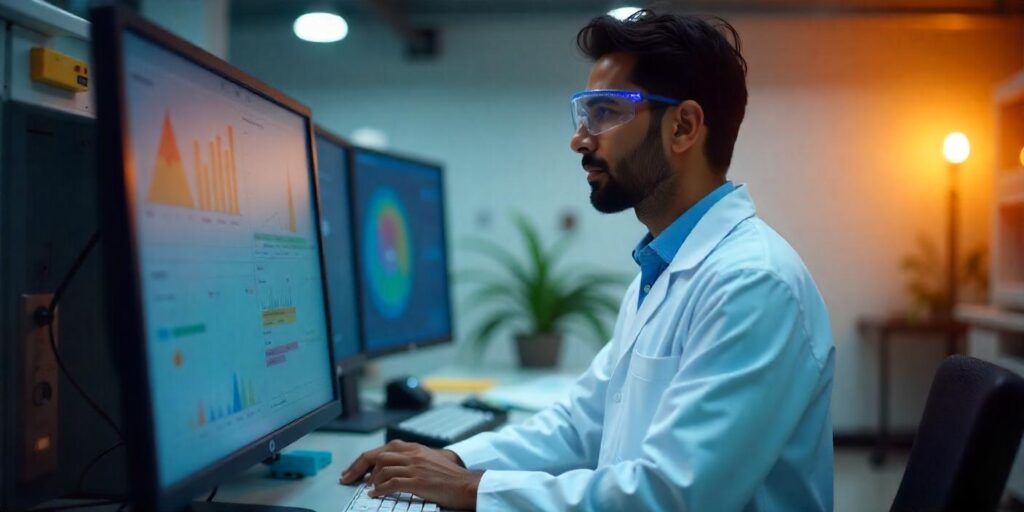
Solution: Adopt systems with built-in access controls, audit trails, and real-time data monitoring. Regularly audit data practices and enforce strict data integrity policies to maintain accuracy at every step. These precautions help ensure that your CQV documentation and data remain reliable and compliant.
6. Change Control
Change is inevitable in CQV, but without proper change control, it can lead to compliance risks and production delays. Managing changes, from protocol updates to new equipment, is essential to keep your process consistent.
Solution: Establish a formal change control process with designated roles for change management. Ensure that each change is documented, reviewed, and approved by relevant stakeholders. This structured approach minimizes errors and prevents unapproved changes from derailing your CQV objectives.
Read More: 9 Emerging Technologies in the CQV Process
7. Impact of Regulatory Compliance
Staying compliant with local and global regulations (FDA, EMA, and other regulatory bodies) is non-negotiable. But regulations evolve, and keeping up can be difficult, especially with international guidelines.
Solution: Regularly update your teams on regulatory changes and engage compliance experts for ongoing support. A dedicated compliance officer or team member can monitor regulatory updates and advise on adjustments to maintain compliance.
8. Validation Challenges in Complex Automation Systems
Automation is rapidly transforming the pharmaceutical and medical device industries, but with this evolution comes new validation challenges, particularly in software integration and data handling.
Solution: Start with detailed validation protocols and engage IT specialists to support automation validation efforts. Run simulations to identify potential issues before full-scale implementation. By accounting for automation specifics upfront, you reduce the risk of costly adjustments later.
Read More: 8 Common Mistakes to Avoid During Commissioning, Qualification, and Validation
9. Time Constraints and Project Delays in CQV
Projects often get delayed due to inadequate planning, resource shortages, or unexpected challenges. In CQV, where time is money, delays can quickly add up in costs and compliance risks.
Solution: Use project management software to keep your project timeline visible and anticipate bottlenecks. Ensure realistic scheduling and conduct regular project reviews to make adjustments as needed. Clear deadlines and early problem detection can make all the difference in keeping your project on track.
10. Integration Between Teams in CQV Projects
CQV projects are collaborative efforts that require input from multiple departments. But without clear communication, misunderstandings can slow progress and introduce errors.
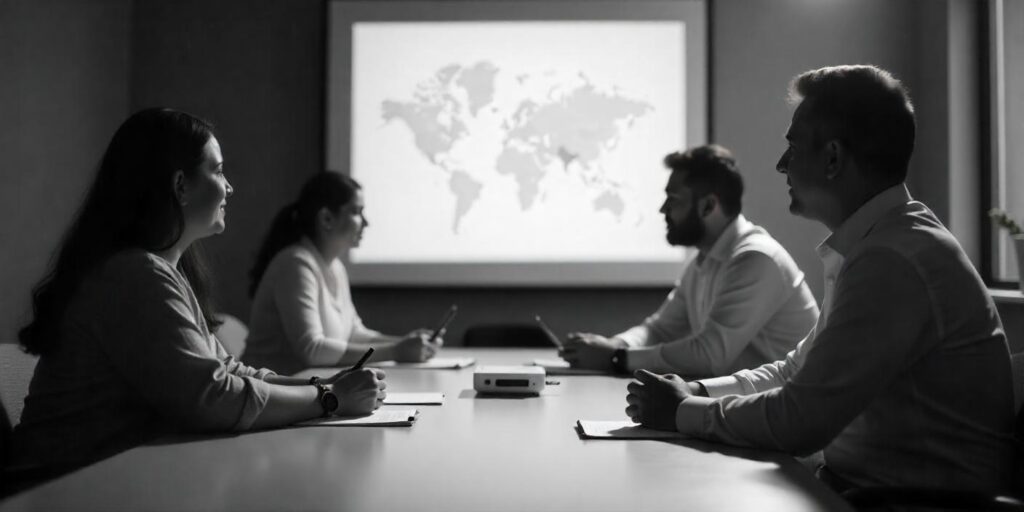
Solution: Hold regular cross-functional meetings to maintain alignment and set clear roles for each team. Strong collaboration and defined responsibilities make it easier for teams to work toward a common goal without stepping on each other’s toes.
How Incepbio Can Assist with your CQV requirements
At Incepbio, we recognize that effective CQV (Commissioning, Qualification, and Validation) processes are critical to maintaining high standards of quality and compliance in pharmaceutical and medical device manufacturing. Our expert team is dedicated to guiding you through every step of the CQV process, ensuring that your facilities, equipment, and systems meet regulatory requirements and industry best practices.
We offer a range of services tailored to your CQV needs, including:
- Comprehensive Assessment and Planning: Our team conducts thorough assessments of your current CQV processes and develops customized plans to address gaps and optimize efficiency. We focus on aligning your CQV strategy with your business goals while ensuring compliance with local and international regulations.
- Documentation Support: We help streamline the documentation process, providing templates and guidance to ensure that all necessary records are maintained accurately and in compliance with regulatory standards. This support helps reduce the burden of paperwork and allows your team to focus on core operations.
- Training and Education: We provide training sessions to empower your staff with the knowledge and skills necessary for effective CQV implementation. Our training programs cover the latest regulatory updates, best practices, and hands-on techniques, ensuring your team is well-equipped to manage CQV challenges.
- Ongoing Support and Audits: After initial implementation, we continue to support your CQV processes through regular audits and reviews. This ensures that your systems remain compliant with evolving regulations and helps identify areas for improvement.
Conclusion: Investing in Efficient CQV Processes for Long-Term Success
Overcoming CQV challenges is essential for any pharmaceutical or medical device company looking to maintain quality, compliance, and customer trust. From documentation to data integrity, the solutions we’ve shared can streamline your CQV journey and support a smoother path to compliance. Efficient CQV practices provide a competitive advantage and protect against costly errors in this heavily regulated industry.
By addressing these top CQV challenges head-on, you’re not only safeguarding your processes but also securing long-term success and reliability for your company.
Authors
-
Shubhankar is a pharmaceutical professional with over 10 + years of experience in Drug Substance (Upstream), Aseptic Batch Manufacturing (Drug Product), Process Validation, and CQV (Commissioning, Qualification, and Validation). He is skilled in managing the qualification and implementation of protocols for URS, DQ, FAT, SAT, IQ, OQ, and PQ for new equipment. Holds sounds knowledge of CSV (Computer System Validation) in compliance with 21 CFR 210/211, 21 CFR Part 11, and European regulations. Shubhankar is experienced in creating cGMP-oriented documentation, including SOPs, BPRs, Calibration Records, and deviation investigations. Expertise in overseeing various validation activities, such as HVAC, Utility, and Process Equipment Validation.
View all posts -
An experienced SEO professional, Adithya is someone fascinated by the art of content creation. He has published over 700 articles under his name. Additionally, he has worked for companies like TCS, Essentially Sports, and holds expertise in the field of digital marketing
View all posts -
Arjun Jha has over 8 years of experience in tech startups, business strategy, and digital and traditional marketing. He’s helped many startups grow by using creative strategies and a deep understanding of the market. Outside of work, Arjun enjoys reading about business, philosophy, psychology, and spirituality, which inspires his unique approach to problem-solving and growth.
View all posts